 |
I compositi termoplastici rinforzati con fibre minerali (GF), sintetiche(CF) o naturali (juta, kenaf etc.) rivestono un’importanza sempre maggiore nella progettazione e realizzazione di componenti strutturali.
|
|
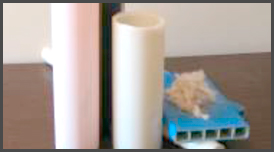 |
|
|
|
|
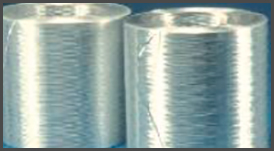 |
 |
In generale le fibre possono essere incorporate in una resina termoplastica allo stato di fibre tagliate o continue. Entrambe le soluzioni hanno vantaggi e svantaggi, anche se esistono nicchie applicative in cui le une o le altre hanno privilegi di accesso. Ad esempio nello stampaggio a iniezione o nella termoformatura a sensibile imbutitura l’utilizzo di fibre tagliate è una necessità. |
|
|
|
 |
La dispersione di filamenti in liquidi altamente viscosi, come sono normalmente i liquidi polimerici, incontra numerose difficoltà. Il goal è di rivestire col polimero tutti i filamenti, uno per uno, altrimenti l’effetto rinforzante va perduto. Si pensi ad esempio ad un ciuffo di 4200 filamenti di vetro di 17 micron di diametro (2400 TEX). Si pensi al fatto che il tempo di permanenza di questo ciuffo in un processore non può essere illimitato, ad esempio non superiore a 10 s, pena la degradazione del polimero o l’eccessiva rottura dei filamenti.
|
|
 |
|
|
|
|
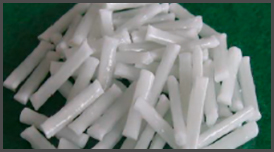 |
 |
Oggi lo stato dell'arte non è compatibile né con un tempo di permanenza molto ridotto, né con la capacità di disperdere i filamenti senza romperli. E’ del tutto normale che filamenti lunghi 4.5 mm all’ingresso diventino più corti di 1 mm nel composito in uscita. Questo fatto può ridurre le proprietà meccaniche del composito fino e oltre il 50%. |
|
|
|
 |
Per ovviare alle limitazioni note dell’arte spesso si utilizzano i c.d. granuli pultrusi, prodotti mediante l’impregnazione continua di roving e la loro riduzione a forma cilindrica e successivo taglio. Questo processo ovviamente è molto costoso e spesso non fornisce risultati adeguati.
|
|
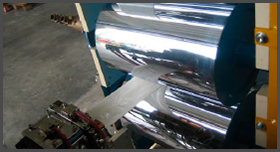 |
|
|
|
 |
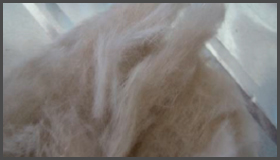 |
 |
Grazie all’azione gentile, anche se energica, della camera di mescolazione il Nexxus Mixing provvede a disperdere uniformemente le fibre tagliate nella matrice polimerica liquida, senza praticamente accorciarle, cioè di fatto rispettando la lunghezza originale. |
|
|
|
 |
Per migliorare ulteriormente le proprietà del composito e disperdere le fibre con sforzi di taglio inferiori a quello normalmente scaricati, Nexxus ha sviluppato un nuovo metodo di preparazione delle fibre chiamato FIBERPREG. |
|
|
 |
L’applicazione è ancora in fase di sviluppo. |