 |
Quando è richiesta una significativa portata circonferenziale, in un estrusore a vite, la qualità “circonferenziale” del fuso, dipende strettamente dal rapporto λ tra flusso circonferenziale e flusso assiale. Se ad esempio il flusso circonferenziale è minimo (tolleranza filetto-cilindro di poco superiore a 0, ad esempio introdotta esclusivamente per evitare contatti), allora la deformazione “circonferenziale” è praticamente nulla e la qualità che dipende da questa deformazione è assente. Se invece il gap tra filetto e cilindro aumenta portandosi a valori >>0 oppure vengono aumentate adeguatamente la velocità della vite o la lunghezza della zona di trascinamento circonferenziale, allora il rapporto tra flusso circonferenziale e flusso assiale aumenterà gradualmente fino a portarsi su livelli >>1, ma in questo caso il residence time medio (Rtav) del materiale aumenta a discapito della qualità e della sua distribuzione.
|
|
|
 |
Zehev Tadmor e Manas-Ica Zloczower hanno sviluppato un’equazione statistica (NPD-Number of Passages Distribution Function) che predice la densità dei passaggi per una popolazione di particelle fluide in funzione del rapporto λ, assumendo che dopo ogni passaggio il liquido venga perfettamente rimescolato (rif.1): |
 |
|
Rif. 1 I. Manas-Zloczower and Z. Tadmor, “The Distribution of Number of Passages over the Flights in Single Screw Melt Extruders”, Adv.Plast.Technol.,3,213, (1983) |
|
|
 |
Nell’eq. 1 k si riferisce al numero probabile dei passaggi delle diverse frazioni della popolazione liquida. L’equazione afferma, ad esempio, che la portata circonferenziale deve essere più grande della portata assiale di almeno 4,6 volte, se si vuole raggiungere la certezza statistica che tutto il materiale sia passato almeno 1 volta attraverso il filetto. Poiché, per dati gap tra filetto/cilindro e velocità vite, la portata circonferenziale dipende dalla lunghezza assiale della sezione considerata, è chiaro che per avere la certezza statistica di un certo numero di passaggi k, il valore λ deve essere proporzionalmente elevato e di conseguenza la sezione di interesse deve avere una considerevole lunghezza assiale. |
|
|
 |
Le verifiche sperimentali hanno mostrato che per avere la certezza statistica che la maggior parte del materiale abbia eseguito almeno 1 passaggio circonferenziale, il rapporto λ deve essere molto maggiore di 4,6 e in alcuni casi spingersi fino a 10 e oltre. Questo perché negli estrusori a vite quasi mai ha luogo una perfetta mescolazione tra due passaggi successivi, assunzione fondamentale della teoria. |
|
|
 |
Di seguito sono rappresentate alcune curve di distribuzione NPD in differenti condizioni di λ, per un range k compreso tra 0 e 2λ utile per impostare curve simmetriche. Le curve riportate di lato mettono in evidenza la larga distribuzione della qualità del prodotto in qualsiasi situazione di λ. |
Curve NPD per alcuni valori λ =5,10,15
e 20-e valori interi k compresi tra 0 e 2 λ. |
|
|
|
 |
|
|
|
 |
Per rapporti λ= 5, 10, 15 e 20, la maggior parte del materiale passa attraverso i filetti rispettivamente 1, 5, 9 e 14 volte. E’ evidente la limitazione che discende dall’impostazione di un valore elevato di λ. Per aumentare λ l’unica via praticabile (a parità di diametro, velocità vite e gap), è di allungare assialmente, come visto, la sezione di mescolazione circonferenziale; ma così facendo si aumentano notevolmente l’energia di mescolazione, il residence time medio e l’investimento nel macchinario. Come anticipato, se è sufficiente che la maggior parte del materiale passi una sola volta, allora λ deve essere uguale ad almeno 4,6. Questo significa, ad esempio, che se la portata assiale è 100 Kg/h, la portata circonferenziale, nella zona di interesse, deve essere almeno di 460 Kg/h. Se invece, nel medesimo esempio, è necessario che il materiale passi almeno 5 volte, è necessario che la portata circonferenziale sia di 1000 Kg/h e così via. |
|
|
 |
Per dirla con linguaggio colorito la distribuzione assiale della qualità “circonferenziale” del fuso è stretta tra due pericoli opposti, entrambi catastrofici. Se λ si avvicina a zero semplicemente non c’è passaggio circonferenziale e la speranza della qualità “circonferenziale” è delusa. Se invece λ è sufficientemente grande da garantire alla maggior parte del fuso il trattamento desiderato (ad esempio 4 passaggi circonferenziali), allora la distribuzione della qualità circonferenziale diventa indesiderabilmente larga. |
|
|
 |
In tutti i casi risolti con l’eq. 1, l’ampiezza della distribuzione qualitativa è notevole. Ad esempio nel caso di λ =4,6 ci sono molte particelle che passano una sola volta e molte che passano 10 volte, mentre nel caso di λ =10, ci sono molte particelle che passano solo 5 volte e molte che passano ben 17 volte, e così via. |
|
|
 |
In generale le particelle liquide che sostano di più nell’estrusore a causa di un eccessivo numero di passaggi circonferenziali, hanno un residence time più elevato e rischiano maggiormente la degradazione termica. |
|
|
 |
Le principali applicazioni, nell’estrusione a vite convenzionale, che risentono negativamente di una distribuzione ampia della qualità del materiale sono essenzialmente tre: a) mescolazione distributiva, b) mescolazione dispersiva, c) degasaggio. |
|
|
 |
Le cose vanno ben diversamente con il canale anulare di Nexxus, in cui il flusso è rigorosamente monodirezionale. |
|
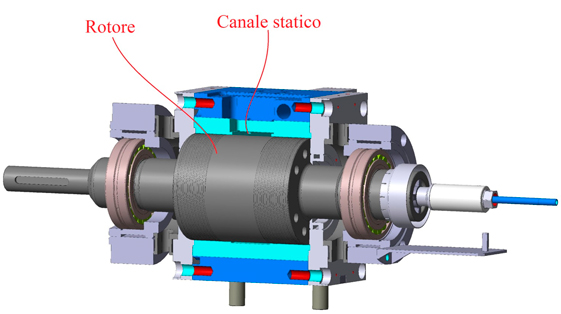 |
 |
Il percorso seguito dalla popolazione di particelle fluide in Nexxus è sempre uguale, per un dato modello, e corrisponde, all’incirca, a 2/3 della circonferenza del rotore. Questo accade sia quando il percorso è lineare (canale liscio) sia quando il percorso è tortuoso (canale con incroci), |
|
|
 |
Nel caso di Nexxus non è necessario ricorrere alla probabilità statistica, per predire la qualità del fuso, in quanto: |
|
- Il tempo di residenza di tutte le singole particelle è materialmente identico e si approssima al residence time medio (Rt(x)→Rtav).
- Quanto detto sopra vale per tutti i tipi di processo: a) mescolazione di polveri o fibre (vuoi dispersiva-elongazionale vuoi distributiva), b) mescolazione reattiva c) degasaggio ecc.
|
|
|
|
 |
Per le ragioni citate la curva di distribuzione della qualità del materiale può essere rappresentata, per Nexxus, come una retta parallela all’ascissa (eq. 2). In altre parole tutte le particelle fluide hanno il medesimo residence time, lo stesso trattamento dispersivo, lo stesso trattamento distributivo ecc. Questa è anche la condizione ottimale per lo standard qualitativo di un prodotto e la sua ripetibilità. |
|
|
 |
Sotto è riportata la rappresentazione grafica di una distribuzione normale standard del residence time nella camera di processo di Nexxus. Come è noto, l’equazione della curva è: |
|
 |
 |
Impostando il valore medio µ =0 e la deviazione
standard σ molto prossima allo 0, per un numero
qualsiasi di particelle, a esempio 1000, avremo:
|
|
|
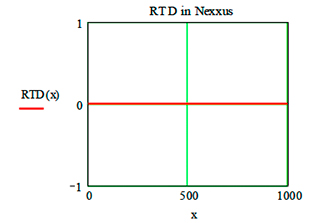 |
|
|
|
 |
|