 |
The devolatilization efficiency of a thin melt film spread over the Nexxus rotor depends on several variables and among the others: the melt film thickness (m), the residence time of the film in the degassing chamber (s), the gas diffusion coefficient D’ (m²/s) through melt etc.. Since D’ is an inverse function of viscosity which relates inversely with melt temperature, it comes out that the characteristic diffusion time λ may be reduced by increasing T.
|
|
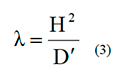 |
where:
- λ = characteristic diffusion time (s)
- H = thickness of the melt film
- D’ = the coefficient of gas diffusion through melt (m²/s)
|
|
|
|
 |
In general temperature increase is an effective way to reduce λ through viscosity as D’ reduces when viscosity is lowered. Therefore it is quite important to secure effective heating in the degassing chamber, in order to contrast cooling down which typically accompanies vaporization. In the Nexxus rotor the heating efficiency is secured by many cartridges powered by slip rings and controlled by a temperature sensor fixed close to the external wall.
|
|
|
 |
The Fick’s law (3) teaches that degassing efficiency is more affected by the melt film thickness rather than the time exposure to vacuum. In other words it is relatively more important to provide a thinner melt film rather than a longer residence time. Nexxus allows for a fine melt film thickness adjustment by mounting different melt spreading dies. Many of such spreading dies range from 0,1 to 0,5 mm.
|
 |
|
|
|
 |
The gas removal from melt, in Nexxus Degassing, changes radically the process efficiency as compared with State Of Art (SOA) degassing in conventional screw extruders. In screw extruders the melt to be degassed faces more drawbacks and for example:
|
|
- Is spread over the barrel by the screw flight when rotating, thanks to the flight clearance. Theoretically the melt film spread over the barrel surface has the same thickness as the flight clearance and one could think that this thickness remains constant over one complete screw revolution. Unfortunately the melt film thickness is continuously waving from a maximum to nearly zero, due to the screw deflection during rotation. As a consequence the degassing efficiency is non uniform.
- The time the melt film is exposed to vacuum circumferentially without changing its structure, due to the shear induced by the flight, is limited to the time needed to pass between two consecutive flights and by the filling factor of the screw. In a square pitched screw this time doesn’t exceed usually fractional seconds, e.g. 0,1 s which is far to be sufficient for complete degassing with a standard flight clearance.
- The flow is two dimensional (some liquid flows parallel to the flight and some other across the flight), sofar the melt film composition changes continuously. As a consequence a very long venting section is needed to gain the statistical confidence that all or most of melt has been vented. This at turn leads to the risk of thermal degradation and a broad venting quality distribution.
|
|
|
 |
Neither of the above drawbacks can occur in Nexxus Degassing where:
|
|
- The melt film thickness remains rigorously constant over the whole time it travels through the degassing chamber. This is due to two main factors: a) the relative position of rotor vs the static plate cannot change as the rotor is rigidly fixed at both ends to powerful bearing groups. Moreover the rotor cannot deflect due to the enormous inertia vs the relatively small pressures existing in the machine. b) There is zero shear between the time the melt film is spread over the rotor and the time it leaves the degassing chamber, thus the melt film composition remains exactly the same over the entire degassing time.
- The melt film thickness can be adjusted in the low range, e.g. between 0,1 and 0,5 mm, by simply changing some modular parts. Due to it, according to Fick’s law, even a relatively small degassing time is sufficient to get complete gas removal in most cases.
- The degassing quality distribution drops nearly to zero, i.e. the ratio of the mean value to any population sample value tends to unity.
|