 |
Looking to the cross section, the red colored melt enters in the mixing chamber, spread over the rotor, in a clockwise direction and fills up the mixing chamber up to a certain circumferential level, depending on the processing target. Downstream, the pumping section provides to discharge the melt through the exit die (extrusion die, Nexxus DEGASSING or others). |
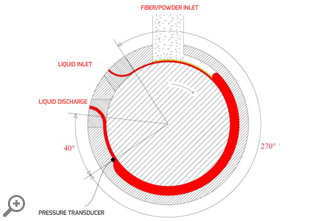 |
|