 |
The spreading die can be easily replaced to achieve the desired film thickness over the rotor (e.g. from 0,1 to 1 mm).
|
|
|
 |
The filling degree of the mixing chamber defines the mixing time which equals the ratio of the accumulated melt volume(Vol) to the volumetric flow rate(Qvol) (Rt=Vol/Qvol)
|
|
|
 |
It is evident that mixing work increases vs mixing time which at turn depends on the filling factor of the chamber, for given material and operative conditions.
|
|
|
 |
The mixing chamber, similarly to all other Nexxus modules, is fully encased into the internal bush wall. The bush can be easily demounted and replaced either for maintenance reasons or for changing the mixing geometry.
|
|
|
 |
The internal bush wall can be designed with different patterns to privilege the type of mixing required by the application. The figures below show some different patterns:
|
|
Single taper bush, for one elongational step
|
Triple taper bush, for three consecutive elongational steps
|
Multiple patterned taper bush, for simultaneous distributive and dispersive mixing
|
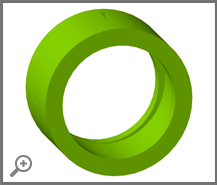 |
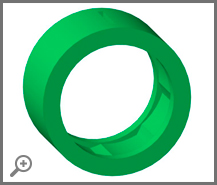 |
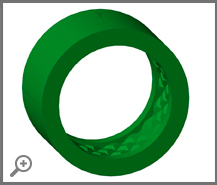 |
|
 |
The bush geometry can be designed as to achieve high quality composites, and for example long fiber reinforced or micro vs nano particles dispersions, etc.
|
|
|
 |
Below a line for production of GF reinforced PP or PA pellets is shown. Fibers well tested in our laboratory unit are for example: glass, carbon, aramid, PET, or natural like jute or kenaf..
|
|
|
|
|
 |
The capability of Nexxus MIXING module to discharge a high mechanical energy without forcing the fibers to follow a tortuous path with many right angle deviations, is one explanation why Nexxus is able to well disperse fibers without breaking down nor shorten.
|
|
|
 |
The Nexxus MIXING module can receive the fibers in different length, either chopped by means of dosing units or endless from bobbins.
|